3D printing allows you to manufacture objects based on computer-aided design (CAD) models. The process is swift, produces lightweight geometric objects, and has low initial fixed setup costs.
Fused deposition modeling (FDM) is the most popular form of 3D printing at home. FDM printers extrude thermoplastic filaments like ABS and PLA through a heated nozzle, layer by layer. Contact By3Design now!
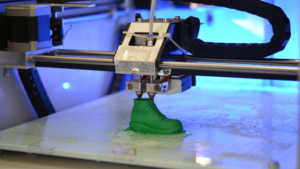
Printing 3D objects requires a unique combination of technical, creative, and analytical abilities. The process starts with a virtual design that is created using computer software or a 3D scanner, which simulates the exact dimensions of the object. This allows for less error during printing, and the designer can correct any mistakes before the printing process begins.
Once the virtual design is complete, it is sliced into layers using software that is compatible with the 3D printer. The sliced file is sent to the printer, which uses a spool of plastic filament as its building material. A motor pushes the filament through a heated nozzle and melts into thin, solid layers that are printed on top of each other until the shape is complete. Depending on the complexity of the model, support structures may be needed to hold the part together or help with stability during printing.
As the technology has become more affordable, many consumers have begun to own 3D printers. These devices can produce a variety of functional objects, including toys, decorative items, and tools. Some users even make customized items for themselves and their home, such as backscratchers or door knobs.
3D printing has also been used to create medical equipment. During the COVID-19 pandemic, hospitals were struggling to keep up with demand for personal protective equipment (PPE) and spare parts for ventilators. This was largely due to a shortage of supplies, which caused some healthcare workers to turn to 3D printers with their own home machines in order to have the PPE and ventilator components they needed.
While some 3D prints are practical and serve a purpose, others are not. Some of the most popular non-functional 3D prints include a replica of a T-Rex, a pecking woodpecker toy, and a sexy, female-shaped key holder. While some of these creations have no use, they are a fun way to experiment with the technology and show off the user’s creativity.
Materials
3D printing technology uses a variety of materials to produce the object you want. Some are specialized for specific purposes, and some are designed to work with a particular printing process.
The most common material used in 3D printing is plastic. It can be used in many different types of objects and comes in multiple colors. It can also be transparent. It is available in a wide range of prices and is widely used for everything from concept models to functional prototypes.
Another popular type of material for 3D printing is metal. It is printed using a process called direct metal laser sintering (DMLS) and is used in a variety of applications. It is popular for aerospace parts where there is a need for a light-weighted and fast manufacturing process. It is also gaining popularity in jewelry and household fixtures.
Ceramics are another type of material that can be printed. They are a solid material that contains inorganic compounds of metal and non-metal with ionic and covalent bonds. They are extremely strong and can withstand high temperatures, making them an ideal choice for technical components. They are also resistant to corrosion and can be molded into complex structures.
A new and emerging type of material for 3D printing is bioink, a liquid that has specialized properties and a high level of elasticity. It is used in a process known as biologically-inspired manufacturing or bioprinting and it can contain stemming cells, growth factors and biomaterials.
Depending on the needs of your print, there are also special materials designed to withstand certain temperatures or have other specific physical properties. For example, if you need a material that can print at a high temperature, there are several filaments such as ABS and PLA that can handle this. If you need a material that is chemical-resistant, there are a number of filaments including nylon and PETG.
There are also a variety of specialty materials for 3D printing, such as wood and metallic materials. These can be combined with other materials to create unique materials. For instance, a print made with wood-bearing filaments can be sanded to a smooth finish or stained and varnished for a natural look. Metal-infused prints can be polished to a metallic shine or oxidized for a patina finish.
Software
The first step in 3D printing is creating a virtual design of an object, which can be made using computer-aided design (CAD) software. This software works like a blueprint for the printer to read, allowing you to make precise drawings and technical illustrations. Alternatively, you can use a 3D scanner to create a digital copy of an existing physical object. After the design has been created, it must be prepared for printing. This is done by breaking down the model into hundreds or thousands of thin, horizontal layers. This is done using special software called slicing, which will produce an STL or OBJ file that can be printed by your 3D printer.
There are several types of 3D printing software available, each with its own advantages and disadvantages. Fusion 360, for example, is a cloud-based program developed by Autodesk that combines parametric, surface, freeform direct, and mesh modeling capabilities. It is popular among professionals and designers due to its versatility and ease of use. It is also compatible with a wide range of file formats and offers many tools to manage the 3D printing process.
Another popular choice is SolidWorks, a 3D modeling software often used by engineering teams for its high-level of precision and accuracy. Its powerful tool set and design validation abilities allow engineers to make improvements before the manufacturing process begins, saving time and money.
A more basic option is Tinkercad, a free CAD software program that works in a web browser. It’s easy to use and offers tutorial resources, making it a good choice for beginners. It can also be used to quickly export models into OBJ and STL files that are compatible with most 3D printers.
Another type of software is a slicer, which converts the digital models into G-code that the 3D printer will use to create the physical object. This software helps to ensure the correct parameters are used for the print, such as layer height and speed. It can also be used to adjust the dimensions of an object, which is important for certain projects. Finally, there is 3D printing hosting software, which allows you to monitor and control your 3D printer remotely. This is especially helpful for businesses with multiple printers.
Printing
3D printing techniques vary in how they form plastic and metal parts. They can also differ in their surface finish, durability, manufacturing speed and cost. Selecting the right process comes down to aligning the advantages and limitations of each technology with your application’s key requirements.
Using 3D printing to make objects involves building them layer-by-layer. To create the first layer, a digital model of the object is made with computer-aided design (CAD) software or with a 3D scanner, which copies an existing object by taking pictures of it from multiple angles. The virtual design is then broken down into hundreds or thousands of thin, horizontal layers. The resulting layers are then printed in sequence to build the object.
FDM, or fused deposition modeling, is the most widely used technique. A nozzle on the printer dispenses small drops of a wax or plastic-like polymer layer-by-layer until the object is complete. The object then cools, and the next layer is added. The result is a three-dimensional object that is strong and relatively lightweight.
Another popular 3D printing technique is selective laser sintering (SLS), which uses a laser to melt and solidify layer-by-layer of powdered metal, such as aluminum, titanium or steel. This method is used in aerospace applications and medical devices.
Once a print job is finished, the object can be removed from the printer and polished or painted to improve its appearance. Alternatively, the print can be cut apart with a saw or burned away with an oxyacetylene torch to remove excess material and make it usable.
Other printing techniques include stereolithography (SLA), which uses a liquid photopolymer resin, and direct metal laser sintering (DMLS), which deposits layers of fine metal powder or wire on top of each other until the desired part is complete.
Inventive designers and entrepreneurs use 3D printing to rapidly prototype products. This allows them to conduct user testing more quickly, iterate designs faster and reduce design risks. More and more companies are adopting this technology, with many implementing it as part of their product development cycles. 3D printing is also being used to tackle major global challenges, such as creating affordable housing. Nonprofit New Story, for example, uses a 33-foot long 3D printer to construct homes in Mexico, Haiti, El Salvador and Bolivia.